當自動化車削單元實施製程控制,僅僅需要 18 天就能回收成本
Equator 可程式設計檢具能協助建立優異的自動化系統,提供軸承加工和零件分類。
美國德州康羅市—Conroe Machine 實現許多加工廠夢寐以求的夢想—全天候採用無人操作的「自控」程序對一系列零件進行車削。該公司將 FANUC 機器人與 Equator 檢具系統進行整合,使用 Renishaw EZ-IO 軟體提供簡單而全面的通信功能,實現 100% 的工件檢測以及對雙軸 Okuma 2SP-250 車床的自動補償。該系統也能對精密加工的工件進行裝箱和堆放作業。該公司宣稱自動化車削系統單元只需短短的 18 天,就能回收成本。
Conroe 證明現今任何一家工廠的年輕一代自動化專家皆能充分使用新技術的潛力,例如該公司的 CNC 程式設計師 James Wardell 和機器人工程師 Jeff Buck 圍繞著Equator所開發出來的相關應用軟體。同一個自動化團隊已著手為客戶打造一個無人化的工件量測/分類系統,這次結合兩台 Equator、一個 FANUC 機器人、一個視覺系統和多條輸送帶系統。在這兩種應用中,Equator 無需使用夾具便能夠快速、經濟有效的量測一系列軸承產品,充分展現出可程式設計比對檢測的價值。
Conroe Machine 是一家相對年輕的公司,由 Murray ‘Tippy' Touchette 在 2000 年所創立,其宗旨是以時下最先進的製造技術生產各種零件。公司隨後快速成長,員工人數達 150 名,擁有一間占地 65,000 平方英尺(6000 平方米)的空調廠房。雖然 Conroe 是一間通用型的工廠,但因為靠近休士頓,因此有相當高比例的業務來自於石油和天然氣產業,主力生產鑽孔零件。該公司的長期業務之一是生產製造泥漿馬達專用的推力軸承產品。每週全天候生產製造數千個這類零件。
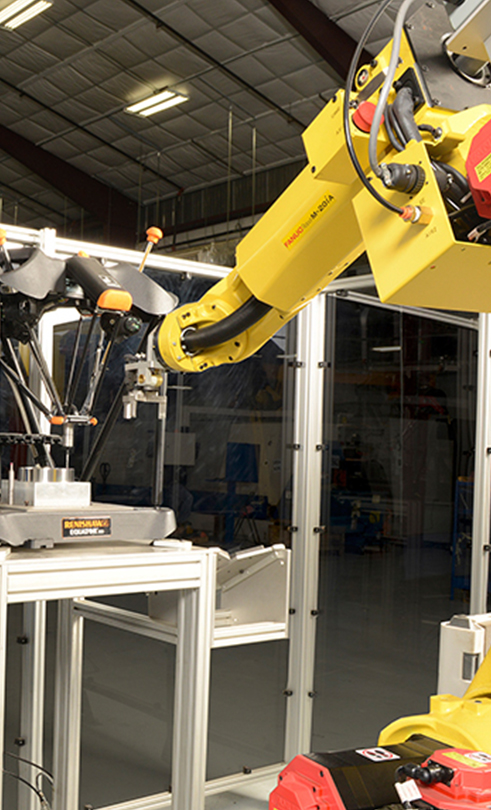
進一步提升自動化水準
目前軸承是在四台 Doosan Puma 車床上進行軸承粗加工,而以往則用這些車床同時進行粗加工和精加工,並且需要四位操作人員進行操作。這些機器現在分為兩個單元,由 FANUC 機器人負責上、下料,並且只進行粗加工作業—這些單元是工廠早期的自動化專案。在精加工車削之前,會先將半成品送到外面進行表面硬化,使其硬度達到 HRC 65,深度為 0.070 吋 (1.7mm)。
James Wardell 說道:「我們每天能利用這兩組單元穩定生產 800-1000 個零件,也就是說每個單元生產 400-500 個。我們安排一位操作人員負責將工件放入生產單元及檢測工件。然而,在這樣的工件數量情況下,還可以仰賴一位操作人員正確檢測,但我們需要更多產量。」
為何選擇 Equator?
他補充:「對於下一步的產量提升,我們規劃一條完全自動化的精密加工製程,包括自動工件裝載、後製程量測、自動刀具補償、工件雕刻,以及工件裝箱/堆放作業。我們對於如何建構此系統的組成,已經擁有一套良好的構想了,除了工件量測技術、CNC 機台類型和刀具補償軟體尚未確定。檢測速度要夠快,必須在 98 秒之內完成才能跟得上工件加工週期時間。一開始,我們考慮過白光雷射檢測,因為它的檢測速度非常快,但工件反射效應太強。我們也考慮過客製化檢具和現場型三次元量床。客製化檢具非常昂貴而且設定時需要非常小心,而三次元量床在速度上表現並不理想。在與 Renishaw 有其他專案合作時,當地的銷售經理 Sheila Schermerhorn,向我們推薦 Equator,認為它是適合的解決方案。」
對我們的加工單元來說,沒有其他現場量測工具的經濟效益可與 Equator 相比擬。
Conroe Machine (USA)
製程控制工具和軟體
Equator 是專用檢具的低成本、靈活替代方案。其採用比對量測方法。經由三次元量床量測標準件進而「標定」Equator,將所有後續的量測與標準件進行比對。標定之後的重現性為 0.00007吋 (0.002 mm)。為補償現場溫度變化,Equator 可隨時重新標定。Equator 使用 SP25 測頭,每秒最多可達 1000 點。測針可存放在內建的六埠交換架中,並透過 MODUS™ Equator 軟體進行編程。Equator 可經由按鈕輕鬆進行手動操作,但在本案例中,也是以 EZ-IO 自動化軟體整合至 Conroe 自動化系統的理想設計。
Wardell 說道:「我們在 2012 年初參加在 Hartwig 舉辦的工廠參觀,見識到 Equator 搭配 Okuma 的龍門型雙主軸車床的實際運作情況。其中使用的自動化方法恰好適合我們的工件類型,車床以 Windows® 為基礎的 OSP 雙路徑控制,也具有一個開放式架構、PC 式的作業平台,這對我們開發自己的自動補償軟體計畫來說極為重要。」
Equator自動化單元中
Wardell 和 Buck 著手組裝一組由 Okuma 2SP-250H、 Equator、雕刻機,以及 FANUC M20iA 6 軸機器人所組成的單元。生產過程中,將待加工的工件(約300個)裝入車床的雙輸送帶。車床的雙門型機械手負責將待加工之工件送至主軸,並將精加工過的工件放置在一條輸送帶上,以供機器人夾取。機器人會將零件放置在 Equator 上進行量測,若量測結果為合格品,就會將其輸送至雕刻機,最後將合格工件裝箱/堆放。
Wardell 補充:「我們自主開發刀具補償軟體,以在 OSP 控制器上執行。Equator 將量測結果以 CSV 檔案格式傳送至軟體,以便在工件偏離公差時補正刀具。」工件每側的加工深度為 0.015 吋 (0.38 mm),公差嚴格限定在 ±0.001吋 (0.025 mm),表面粗糙度為0.008 吋(0.5 μm)。工件的外徑尺寸範圍從三到六英吋不等Wardell 表示:「Equator 能輕鬆且有效的在我們的公差範圍內執行量測作業。」
製程控制
「我們的 外徑/內徑 幾乎是保持不變的,半徑偏差量僅為 5 μm。依尺寸分批加工工件,因此能將夾爪和其他工具的轉換降至最低。Equator 的量測速度能輕易跟上製程的腳步。因我們廠房空調控制為 72 °F (22.2 °C),一天只須重新標定一次。」
檢測原理和靈活的自動化
工件的量測方法出乎意料地簡單。Wardell 說明:「我們製作一個中央有孔的鋁塊,並將其放在 Equator 治具基板的中心點。用其決定我們的中心,並設定座標系統。將每個零件放置在鋁塊的中心。我們以接觸方式取得工件中心,然後對其他特徵進行表面掃描。我們已規劃出一套量測過程,操作時不須更換工件夾具,或測針。機器人可透過 Equator 的 EZ-IO 自動化軟體,依工件選擇量測程式。我們知道必須量測哪些重要特徵,才能確保工件在公差範圍內。」

量測/分類使用過的工件
車削加工單元目前每天能製作出約 600-700 個成品件,因此與之前的兩個單元相比,現在只需使用一個單元即可。現在則為客戶開發一項工件分類系統。Wardell 和 Buck 依據 Touchette 所草繪的概念圖,為使用過的泥漿馬達止推軸承產品,開發出一套量測和分類系統。
在油田機械維修廠中,常需要將使用過的馬達拆解、翻新並重新使用。Wardell 說道:「客戶以往是以目視方式檢測使用過的馬達,以判斷其零件是否能重新使用,他們知道這樣總難免會丟棄一些良好的零件,換言之就是丟掉金錢我們希望為他們提供一套隨插即用的量測和分類序系統,避免人為主觀判斷,以便能再利用更多良好的零件。」
在撰寫本文時,Buck 和 Wardell 仍在開發該系統中,它由兩台 Equator、一具 FANUC LRMate 200iC 6 軸機器人、多條輸送帶系統、一套 FANUC iR 視覺系統和一組供機器人手臂使用的 ATI 快速換刀機所組成。視覺系統將待量測的零件編號以及需要執行的程式告訴 Equator。量測完後,將合格品放在適當的輸送帶上,不良品則放置在廢品輸送帶上。
Buck 說道:「我們設計的這個系統可以用卡車裝貨運送,且讓馬達廠人員的非常容易使用該系統—只需啟動電源,將零件裝載進輸送帶即可。」
Wardell 補充:「對我們的加工單元來說,沒有其他現場量測工具的經濟效益可與 Equator 相比擬。我們希望為客戶所提供的整合式服務,能為我們公司在此業務領域開創出一條新的途徑。」